USP: Modelo de viseira de proteção é produzido por indústrias no combate à COVID-19
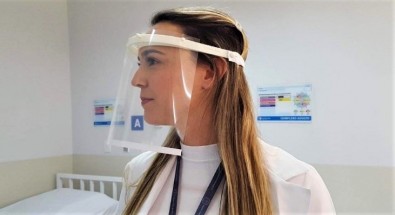
Máscaras do tipo face shield se tornaram um equipamento de máxima importância para agentes de saúde que atuam na linha de frente do combate à COVID-19, doença causada pelo novo coronavírus. Esses dispositivos, semelhantes às viseiras de capacetes de motociclistas, constituem uma primeira barreira física que protege médicos, enfermeiros, técnicos de enfermagem, fisioterapeutas e outros profissionais do contato com as gotículas infectadas pelos vírus exaladas pelos pacientes. Por baixo delas, é necessário usar as máscaras convencionais.
A necessidade de produzir rapidamente máscaras face shield em grande escala mobilizou vários grupos que trabalham com manufatura aditiva, que utiliza impressão 3D e técnica denominada FFF (fused filament fabrication). Conectados pelas mídias digitais, esses grupos formaram uma rede mundial nas duas últimas semanas e já estão fornecendo máscaras a partir do modelo “Prusa”, um design de uso livre criado pelo inventor tcheco Josef Prusa.
Um dos integrantes dessa rede é o Grupo de Pesquisa em Manufatura Aditiva e Design for Assistive Tecnology, coordenado por Zilda de Castro Silveira, professora do Departamento de Engenharia Mecânica da Escola de Engenharia de São Carlos, da Universidade de São Paulo (EESC-USP), e pesquisadora do Núcleo de Manufatura Avançada (NUMA).
O NUMA conta com apoio da Fundação de Amparo à Pesquisa do Estado de São Paulo (Fapesp), por meio do Projeto Temático “Estudo, desenvolvimento e aplicação de processo híbrido: Manufatura Aditiva (Ma) + High Speed Machining/Grinding (HSM/G)”, coordenado pelo professor Reginaldo Teixeira Coelho. O núcleo também participa da iniciativa o Departamento de Fisioterapia da Universidade Federal de São Carlos (UFSCar).
“Em nossa primeira semana de trabalho, produzimos 210 máscaras face shield para a Santa Casa de São Carlos. Esse movimento rápido e intensivo impulsionou a indústria de plásticos a adotar o mesmo modelo de projeto para atender em larga escala a demanda dos hospitais”, diz Zilda de Castro Silveira à Agência Fapesp.
Entrega
Segundo a pesquisadora, empresas de São Paulo, Minas Gerais, Paraná, Santa Catarina e Rio Grande do Sul, filiadas à Associação Brasileira da Indústria de Ferramentais (Abinfer), começaram a produzir as face shield nesta semana. A expectativa é que sejam entregues 400 mil máscaras para o Ministério da Saúde na próxima semana. “Para isso, estamos dando todo o nosso apoio”, afirma a pesquisadora.
Uma das questões relacionadas a peças impressas por 3D é a porosidade. “Devido à estruturação física das peças, camada por camada, os objetos fabricados por técnicas aditivas possuem porosidade maior do que aqueles produzidos por técnicas convencionais. Isso não compromete a função de barreira física da peça, mas a torna mais vulnerável à contaminação”, ressalta Silveira.
“Para reduzir o problema, aplicamos acetona, que, por reação química, auxilia na redução da porosidade superficial. E, para reforçar a descontaminação, foram conduzidos, junto com a Santa Casa e a empresa Sterileno, testes de esterilização com peróxido de hidrogênio [H2O2], que se mostrou eficiente. Dessa forma, esse procedimento de desinfecção foi adotado pela Santa Casa para esterilização das máscaras face shields”, completa.
As instituições que receberem as peças fabricadas pelas indústrias poderão aplicar esse mesmo procedimento – a esterilização com peróxido de hidrogênio – para reutilizar as máscaras após cada uso.
Com informações do governo do Estado de São Paulo